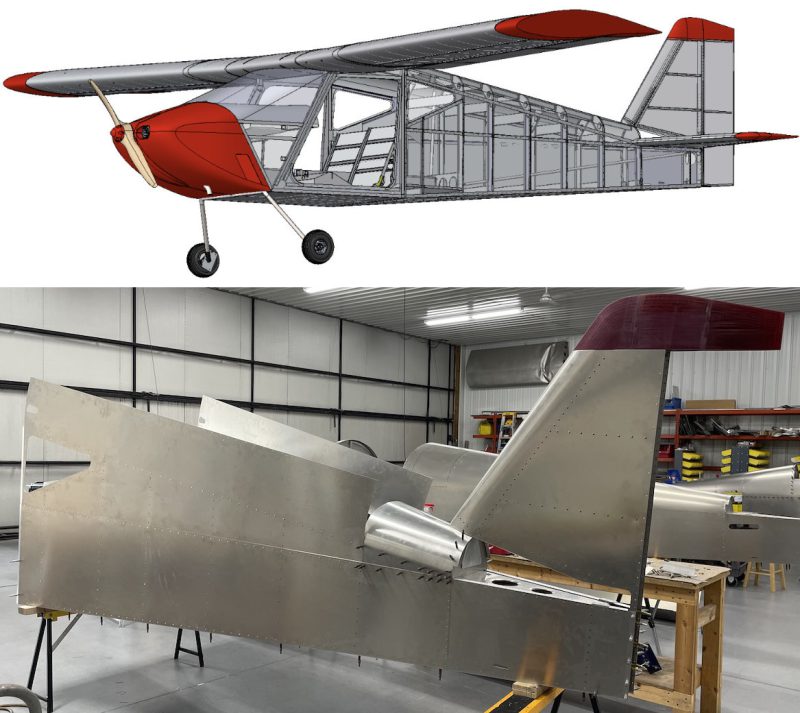
Sonex is pleased to provide this update on the progress of the Sonex Highwing! The Highwing continues to generate huge interest with prospective customers and we have been diligently working to bring the new aircraft design to fruition.
Prototype Construction Has Begun:
Sonex Highwing prototype construction has begun and the tailcone of the aircraft is nearly complete. At AirVenture Oshkosh 2024, our goal is to have the Highwing prototype available for prospective customers to try the cockpit on for-size.
MOSAIC and Updated Specifications:
While finalized MOSAIC Light Sport Aircraft regulations will probably not be released until 2025, the proposed regulations, submitted comments to the NPRM from pilots and industry, and the FAA’s unofficial reactions to those comments offers a reliable set of baseline specifications for the expanded LSA rules that may be expanded even further in the final rule. Since our February ’23 update, we have received a number of comments urging Sonex to design the Highwing to the new regulations.
Looking at the structural requirements to meet our two-place aerobatic load factor design goal, the Sonex design team has concluded that the Highwing can expand beyond the current LSA max gross weight at Utility Category, at-least when using higher horsepower engines such as the 130 hp UL Power UL350iS that will be installed in our first prototype. During flight test of the first Highwing prototype, Sonex test pilots will be conducting Vx and Vy testing at reduced throttle settings to simulate performance with lower powered engines. While this will not be an accurate simulation for Rotax powerplants with reduction drives, these tests will give a fairly accurate representation of the power and torque curves of UL Power, Jabiru and AeroVee engines between 80-120 hp.
At this time, the Estimated Weight Specifications for the Sonex Highwing are as-follows:
- Empty Weight: 800 lbs.
- Aerobatic Category Gross Weight: 1230 lbs.
- Limited Aerobatics Weight (+5.5, -2.5 G): 1340 lbs.
- Utility Category Gross Weight: 1500 lbs.
Current Weight & Balance Examples (Estimated):
- Utility Category: Max Gross Weight Loading (No BRS Installed)
- Empty Aircraft Weight: 820 lbs.
- Fuel: 30 Gallons (180 lbs.)
- Baggage: 80 lbs.
- Pilot: 220 lbs.
- Passenger: 200 lbs.
- Utility Category: Max Gross Weight Loading (with BRS Installed)
- Empty Aircraft Weight (not including BRS): 820 lbs.
- BRS: 40 lbs.
- Fuel: 30 Gallons (180 lbs.)
- Baggage: 50 lbs.
- Pilot: 210 lbs.
- Passenger: 200 lbs.
- Aerobatic Category (+6, -3 G): Max Gross Weight Loading (No BRS Installed)
- Empty Aircraft Weight (short wing tips installed): 800 lbs.
- Fuel: 10 Gallons (60 lbs.)
- Baggage: None
- Pilot: 200 lbs.
- Passenger: 170 lbs.
- Limited Aerobatic Category (+5.5, -2.5 G): Max Gross Weight Loading (BRS Installed)
- Empty Aircraft Weight (short wing tips installed): 800 lbs.
- BRS: 40 lbs.
- Fuel: 15 Gallons (90 lbs.)
- Baggage: None
- Pilot: 210 lbs.
- Passenger: 200 lbs.
Sonex Highwing prototype tailcone at its current state of construction, shown here with the verical tail test fitted. Note that the tail tip is taller than its actual installed height — this tip is a 3D printed plug for the fiberglass part mold.
View of the Sonex Highwing prototype at the fuselage break showing the baggage area and tailcone structural members.
Cutaway view of the baggage area in the Sonex Highwing CAD model showing the baggage floor installation along with the seat back support cross-tie.
Sonex shop staff members Tony Jones (at-left) and Cris Nash standing in-front of the Highwing tailcone at the approximate location of the seats. Note that the Fuselage structure can be seen on either side of Tony and Cris yet their shoulders are not touching, even with their arms crossed to make themselves as-wide as possible. The Sonex Highwing has an interior cockpit width of 42 inches.
BRS Installation:
Installation of a BRS will be optional and the system will be installed in the baggage compartment to exit through the top window in the baggage compartment. For the most useful load capability, exclusion of the BRS installation will allow baggage capacity up-to 90 lbs. For aerobatics, keep in-mind that the Sonex Highwing will feature jettisonable doors for pilots that choose to wear a parachute.
More Seating and Baggage Area Details:
As almost every part for the Sonex Highwing is now designed, there’s a lot more detail available in our SolidWorks model vs. what was shown in February 2023:
- The baggage area is as shown in our last update, but now has a floor. This floor adds to the box structure required for fuselage strength and allows the higher baggage weights allowable in the Highwing, while protecting the belly of the aircraft from baggage-related dents.
- The crosstie at the top of the seat back shown in our last update has now been lowered, sitting at the top of the control column tunnel, and there is a forward baggage wall between the cross tie and the floor.
- As discussed in our last update, the Highwing will have hinged adjustable seat backs. We have designed the seat hinges so that they can fold forward without removing the seat cushions. The seat back hinge attachments can also be easily moved between two stations fore and aft, allowing pilots to adjust their distance to the rudder pedals, stick and instrument panel. Both the fore and aft station allow a range of seat back angle adjustments and the seat backs are easily removable because of the adjustable hinge stations.
Cutaway view of the Sonex Highwing cockpit and baggage compartment. Note that the pilot’s side seat back is shown installed in the forward hinge mount position while the passenger side seat back is installed in the aft hinge mount position. Seat back hinge installation can be easily changed via quick release pins and the seat back can easily be removed from the aircraft to ease loading of baggage or other cargo.
View of the cockpit with both seats folded-down. Note that with a center control stick installed, both seat backs can fold all-the-way down. The geometry of the seat back hinges allow folding with out the need to remove the seat cushions. The seat adjustment supports can be seen in this view, mounted to the seat backs with piano hinge.
Just Sitting Around — Those Controversial Throttle Quadrants:
The throttle quadrant installations shown in our last update created quite a stir as prospective builders felt they would get in the way of the cockpit doorway. After studying the seating positions in the Highwing in more detail, which involved a lot of time “just sitting around” in our current aircraft designs (actually flying some of the time, of course), we’ve concluded that the throttles can be much closer to the instrument panel and actually make the positioning more comfortable than our current aircraft. We’ll undoubtedly make minor adjustments in the positioning of the throttle controls once the prototype cockpit is constructed, but you can be assured that they will not be as-far aft as pictured in our February 2023 update.
A Ceiling to Save Weight:
Another change since our last update involves the cockpit ceiling. The Highwing cockpit will have a ceiling under the outside skin of the aircraft. This eliminates heavy and expensive machined angle wing root fittings by carrying wing torsion loads through the cockpit to the rear spar and will ultimately save weight in the airframe while improving its strength and reducing cost. There will still be greenhouse windows: two windows instead of one large window. The ceiling does not extend to the bottom of the main wing spar and rear spar carry-through members, so headroom in the aircraft will still be very good. Distance from the seat bottom with a 1” cushion to the ceiling will be 40.25 inches.
The single large skylight originally shown in our last udpate has been separated into two skylight windows to allow the installation of a structural cockpit ceiling.
Cutaway view of the Sonex Highwing looking up at the cockpit ceiling. The ceiling is raised relative to the main wing spar and rear spar carrythrough allowing good clearance for tall pilots. distance from teh seat bottom to the ceiling is 41.25 inches — a 1 inch seat bottom cushion would give 40.25 inches of clearance.
Wing Joints all Dressed-Up to Save Weight and Cost:
The Sonex Highwing will utilize ties and cuffs to lighten and improve the strength of the removeable wing joints. The original plan for wing joint knuckles has been abandoned in-favor of traditional bolted wing ties, like those used on the SubSonex. There are a few reasons for this:
- Due to the nature of the high-performing Sonex spar cap’s shape, the knuckle fittings would have still needed the strain-matching steps used in SubSonex wing ties. Combining the relatively complex 5-axis machining required for those wing tie steps with single-bolt interlocking knuckles would have drastically increased machining time, complexity, and cost while making the wing joint heavier than it needs to be.
- Knuckle joints like those originally planned are difficult to match within typical machining tolerances such that slop in the wing joint is eliminated. The through bolt has to be very close-tolerance and the space between knuckles have to be close-tolerance as-well, further increasing production cost and complicating ongoing maintenance of the aircraft.
Similar to the addition of a cockpit ceiling, we have further reduced weight in the wing joints by adding cuff strips between the inboard and outboard wing skins. These cuffs consist of strip of thin sheet metal approximately 3 inches wide that wraps around the wing joint and bridges the gap between the inboard and outboard wing panels. These cuffs will transfer the torsional load between the inboard and outboard wing skins allowing the elimination of heavy extruded angle wing rib fittings at the joint. This change reduces weight and cost of additional machined parts while reducing drag and improving the aesthetics of the wing joint.
This departure from the originally planned knuckle fittings has a lot of advantages as described above, however, it will mean that wing installation and removal will involve a lot more fasteners. The cuff strips will install with nut plates installed in the wing skins and will require a number of screws installed into anchor nuts in the wing skins. Each wing tie fitting (4 fittings on each side of the aircraft) will require the use of 4 bolts (16 bolts per wing panel), and the rear spar connection will have 2 bolts on each side of the aircraft. While we recognize that there are a certain number of customers that want extremely fast wing installation to be able to avoid hangaring the aircraft, the major purpose of the removable wings is to reduce the build space required for the aircraft (can be built in a single-car garage), make it easy to transport from your garage to the airport during the build process, and to facilitate shipping of Quick Build Kits and completed aircraft via trucking and sea freight. Similar to the SubSonex, wing installation or removal on the Sonex Highwing will take less-than an hour.
As we progress on the prototype’s construction and design, and its capabilities come into sharper focus, the Sonex team’s excitement for this new product is growing, and we feel it will capture even more attention from prospective customers with the changes outlined above. We hope to see you at EAA AirVenture Oshkosh 2024 as we show this aircraft for the first time!
Transparent view of the Sonex Highwing’s structural details.
View of the Sonex Highwing in tricycle gear configuration. A tri-gear prototype will be constructed after the completion of the current prototype which will be equipped as a taildragger.
View of the Sonex Highwing aileron, elevator and flap control systems. The control stick frame design allows quick and easy conversion between center stick and dual stick installations, as-well as a single pilot’s side stick only, etc.
Sonex Highwing prototype under construction.
|
Sonex Highwing Estimated SpecificationsSubject to change without notice
* Sonex Highwing features easily interchangeable wing tips for different span configurations. |